Established in 1992 with a registered capital of $5.2 million USD from Australian sole-ownership enterprises, and boasts a 72,000 square meter factory zone. - Custom Injection Molding Machine Manufacturers
CSD-S Servo Motor Series Injection Molding Machine
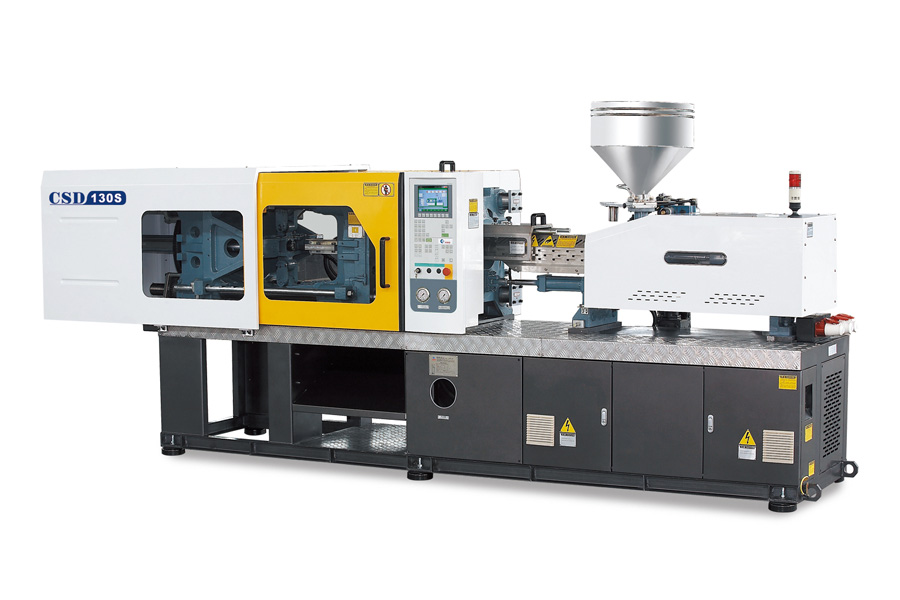
In some cases, the sprue may not fully solidify, and the result is stress cracking.Controlling sprue solidification on injection molding machines involves modifying the flow of plastic through the mold. The sprue ejector pins are connected to the parting line by the parting line. In this way, the sprue solidifies in the cavity, which contains the solidified sprue plastic 10. These plastics may also be separated from the part by an ejector mechanical system or a stripper plate.Injection molding machine dwell pressure can be controlled by adjusting the speed of the moving screw. It's crucial to maintain the proper balance of clamping force and filling pressure, otherwise the molded product may show imperfections and burrs.While gas injection helps the plastic to expand and fill a mold cavity, it's also essential to consider the volumetric shrinkage of plastic, which can make it harder to control the gas.
To compensate for the plastic contraction, injecting gas into the mold cavity can help the plastic continue to expand during the cooling cycle. This is known as the full shot process.The first step in the injection molding process involves mixing dissolved PBA into the molten polymer. The molten polymer then passes through the mold's cavity and is injected into the mold cavity at a given pressure and rate. The next step is to manage the dwell pressure after molten plastic fills the cavities on an injection molding machine.Controlling ejector pins is an important part of the injection molding process. It's necessary to keep these pins at an accurate depth to prevent parts from hanging or "skid-marking" them. Moreover, uneven ejector pins can cause aesthetic issues, particularly for parts with thin walls. They can cause depressed engravings and uneven thicknesses.
One way of controlling ejector pins on an injection mold machine is to have a switch that determines the starting and ending positions of the pins. For example, the start position of the pin is set at position A, and its end position is set at position B. Once the ejector pins reach their completion positions, they vibrate and cause a delay in the process. This will cause the cycle time to increase.To control ejector pins on an injection mold machine, adjust the gate and the feed system to optimize the flow of molten plastic. Then, set up a suitable cooling system to transfer heat away from the melt and keep the cooling rate within limits. Moreover, when designing the mold, analyze the ejection resistance to create the right mold. Lastly, make sure to add the right ejector pins and control the expansion of the gate. By doing so, you can ensure that the part is ejected without leaving a pin mark on the gate.