Established in 1992 with a registered capital of $5.2 million USD from Australian sole-ownership enterprises, and boasts a 72,000 square meter factory zone. - Custom Injection Molding Machine Manufacturers
Cap Mold
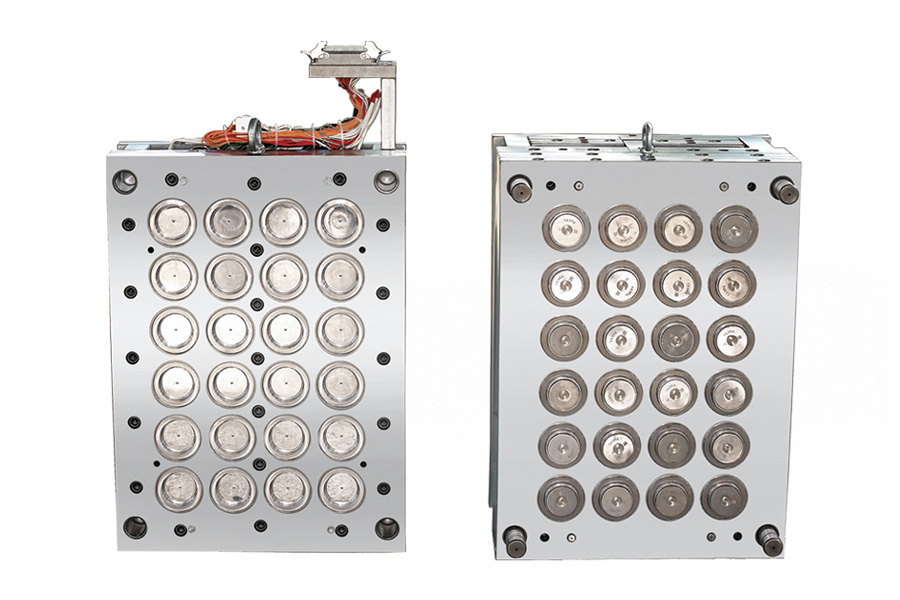
It can be found in the corner of the scribe region on the wafer substrate.Aside from the obvious reason for chamfering the edges, it can also be used to improve productivity. By allowing a small cross-sectional area, the package will be stronger than would be the case if the encapsulant had the same cross-sectional area. In addition, the process will also maintain the hermeticity of the semiconductor element.This can be achieved by using a chamfering tool that can round the corners of the encapsulant with minimal effort. Using the Chamfer tool, you can also control the end point of the chamfer. For instance, if you want to move the end point to the first vertex of the next edge, you can do so with a 1.0 value. You can also chamfer the encapsulant at different angles.The manufacture of plastic parts with undercuts is a challenge for molders.
Undercuts are recessions or protrusions in the part and help to prevent it from sliding away from the mold.Undercuts can be molded in several ways. One way is through a hot runner injection molding process. This is an advanced technology that eliminates regrind waste. A hot runner is a machine that injects molten liquid plastic directly into the mold cavities.Another option is to use a collapsible core. This technology has made it possible to reduce the cost and cycle time of undercut molding. Collapsible cores are usually sized to produce the undercut shape. Depending on the type of undercut, these cores can be used for slots, dimples, or threads.An air poppet is a device that is designed to help eject the cap mold. It works by using a small amount of air pressure to break a vacuum that is formed during the molding process. The use of a poppet can also help you to overcome a variety of vacuum problems that may occur during the process of molding.Air poppets can be used to eject plastic parts from an injection molding machine.
They can be found in a variety of sizes and specifications. You can also get custom-made poppets. These poppets can be used in either an ejector pin or an air valve.In order to use an air poppet, you need to install a special airway in your mold. This type of ejector is easier to use than a normal ejector pin.The optimal placement of cooling channels in a mold is a complex juggling act. One must consider the temperature of the materials, as well as the mold's acoustics. Getting this right can make or break a molding process. The best route to go is to consult an industry expert. For a fee, analysts will recommend a path based on a thorough analysis of the mold and the surrounding environment. Having a solid plan in place is half the battle. The next challenge is executing it. Not to mention the pitfalls associated with the process itself. With the assistance of a good estimator, the tiniest of hiccups can be avoided. If you're not an engineer, or even an aspiring one, a seasoned pro can do the dirty work.