Established in 1992 with a registered capital of $5.2 million USD from Australian sole-ownership enterprises, and boasts a 72,000 square meter factory zone. - Custom Injection Molding Machine Manufacturers
Cap Mold
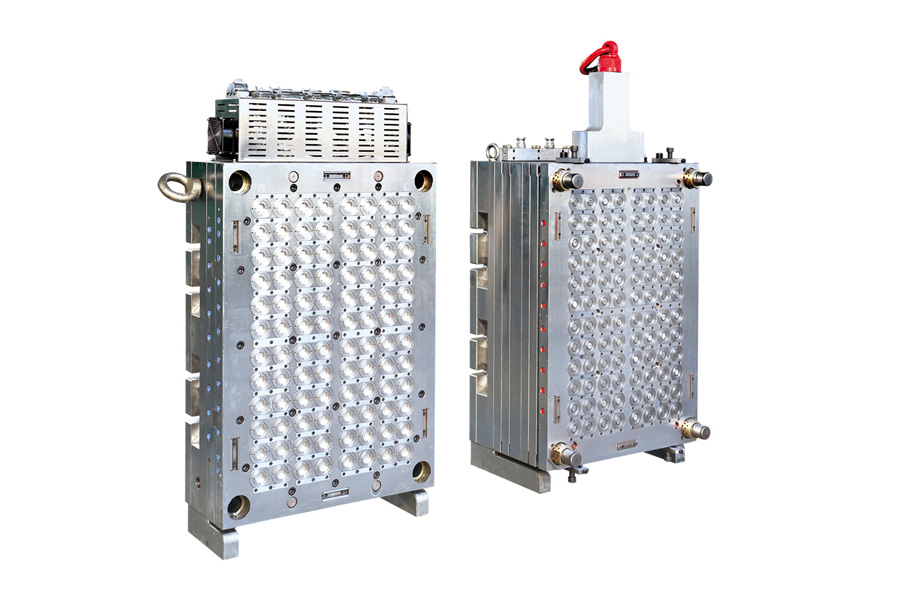
The mold compound 210 is bonded to the die 206 and to the lead frame 205. The cap 220 is attached to the die 206 by an adhesive 217, and the cap is attached to the die with a second adhesive 216.The mold 300 is a device used in the molding process. It works in conjunction with the substrate 200 to produce an array of packages. It has two sections: an upper mold section 302 and a lower mold section 304. The former is designed as a removable cavity bar, while the latter serves as a rigid mold.The upper mold section 302 includes a plurality of extensions 230 that extend from the corners of the mold body. The extensions preferably do not extend beyond the edges of the substrate.When creating a custom cap mold, there are several options for creating the right look. One option is to use a series of fast molds. These molds are made to fit the individual head of a client without any hassles or guesswork.
The fast molds have been tested and proven to work for years. Another option is to use Superhairpieces' caps. These molds are available in 18 different sizes and contour sets, so you can choose the right one for each individual client. The caps are labeled with the correct measurements, which makes it easy to place them on a client's head.Solder mask 116 protects the conductive traces of the semiconductor dies. This protective cover is formed by the transfer molding or injection molding processes. In addition, they have chamfered corners that expose the corners of the substrate. When the substrate is handled, the solder mask at these corners is susceptible to cracking, especially for larger size packages.The solder mask is a thin layer of polymer that is usually green in color. It protects the copper underneath from exposure to the environment and prevents oxidation. It also prevents metal whiskers from growing on the PCB, which can cause shorts.
When properly designed, a solder mask can prevent oxidation of the copper and also extend the shelf life of the component.One of the key factors in cap molding production is cooling time. It can account for more than 80% of the entire cycle time. The amount of time required to cool a cap varies by material, cycle type, and part shape. Figure 1 presents an equation that can be used to estimate cooling time.The wall thickness and material selected for the mold play important roles in determining the cooling time. The mold design engineer must ensure that cooling channels are placed in the best possible positions to maximize cooling efficiency. In addition, the process engineer must ensure that parts are filled as fast as possible. If there is not enough cooling energy available during the filling and pack/hold phases, parts can freeze.