Established in 1992 with a registered capital of $5.2 million USD from Australian sole-ownership enterprises, and boasts a 72,000 square meter factory zone. - Custom Injection Molding Machine Manufacturers
Designing a cap mold for a specific product involves several steps, which may vary depending on the complexity of the product and the specific requirements of the mold. Here are some general guidelines for designing a cap mold:
1.Understand the product requirements: Before designing the mold, it's important to understand the requirements of the product that the mold will be used to produce. This includes factors such as the size and shape of the cap, the type of material it will be made from, and any functional or aesthetic features that are required.
2.Choose the appropriate mold type: Cap molds can be designed in several different configurations, such as two-part molds, hot runner molds, and cold runner molds. The choice of mold type will depend on factors such as the material being used, the complexity of the cap design, and the required production volume.
3.Determine the gating and runner system: The gating and runner system is responsible for delivering molten plastic to the mold cavities. The design of the gating and runner system will depend on factors such as the number and location of cavities, the viscosity of the plastic, and the desired cycle time.
4.Create the mold design: Once the gating and runner system has been determined, the mold design can be created. This involves designing the mold cavities, the cooling system, and any ejector pins or other features that are required to release the cap from the mold.
5.Prototype and test the mold: Before going into full production, it's important to prototype and test the mold to ensure that it produces caps that meet the required specifications. This may involve making adjustments to the mold design or the production process to achieve the desired results.
6.Optimize the production process: Once the mold has been tested and approved, the production process can be optimized for efficiency and quality. This may involve adjusting factors such as the temperature, pressure, and cycle time to achieve the best results.
Cap Mold
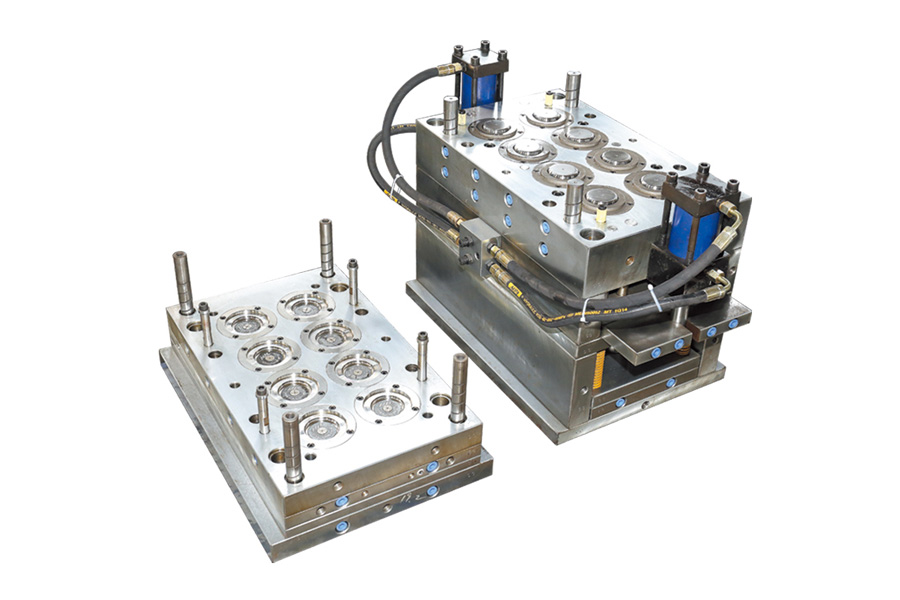
Cap Mold
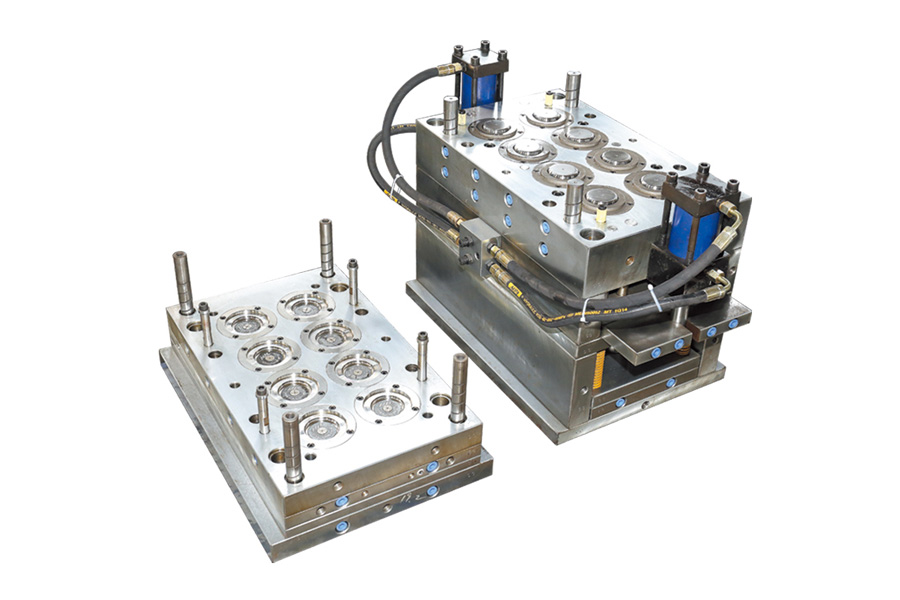